Brushed Permanent Magnet DC Motor
Engineered for smooth operation, they offer a cost-effective solution for industries requiring dependable power in compact, space-saving designs.
With a proven track record of durability, these motors are ideal for use in automotive, robotics, home appliances, and many other sectors.
- Voltage: 24V/130V
- Rated Torque: 0.4-130N·m
- Efficiency:72%-83%
- Insulation Class:B/N
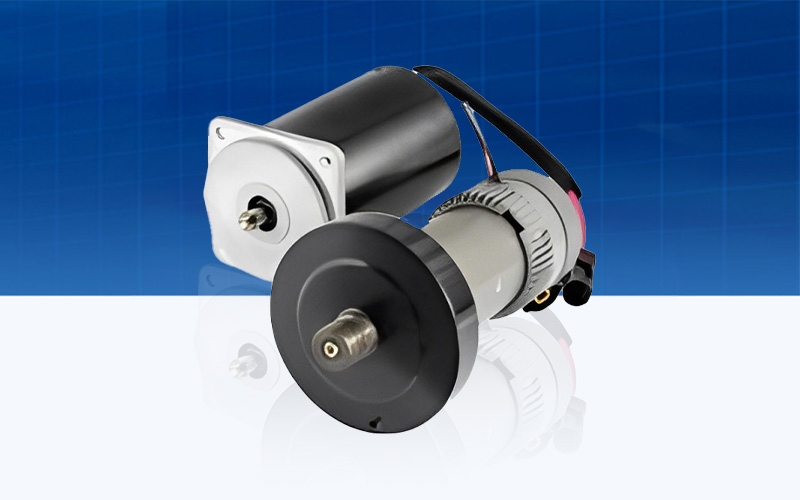
PMDC Brushed Motor Structure
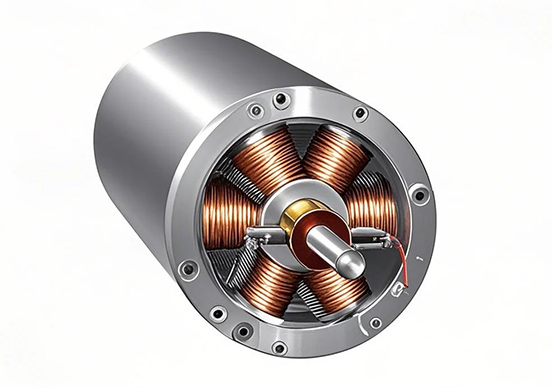
- Stator: Fixed part with field magnets providing magnetic flux.
- Rotor: Rotating part with the armature and windings.
- Commutator: Switches current direction to ensure continuous rotation.
- Brushes: Transfer current between the stator and commutator.
- Shaft: Connects to the rotor, transferring mechanical power.
- Bearings: To ensure smooth rotation, support the rotor shaft.
By Rotor Type
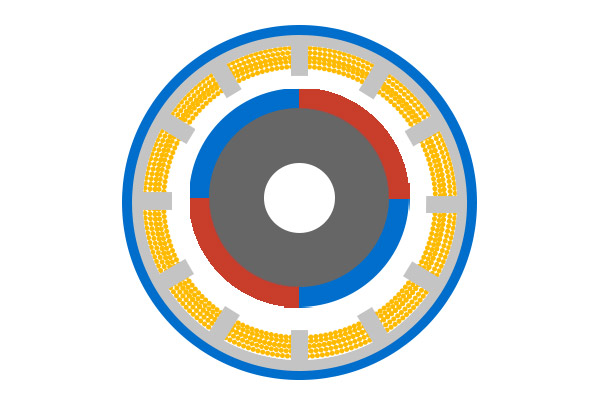
Slotted Type
- Armature slots increase winding surface area for efficiency.
- Cost-effective design suitable for various industrial applications.
- Widely used where efficiency and cost are critical.
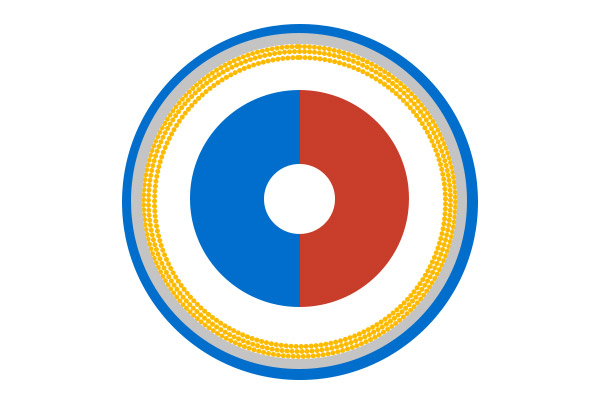
Slotless Type
- No slots on the armature for smoother operation.
- Windings placed directly on the rotor surface.
- Ideal for robotics and precision equipment applications. Inquiry now
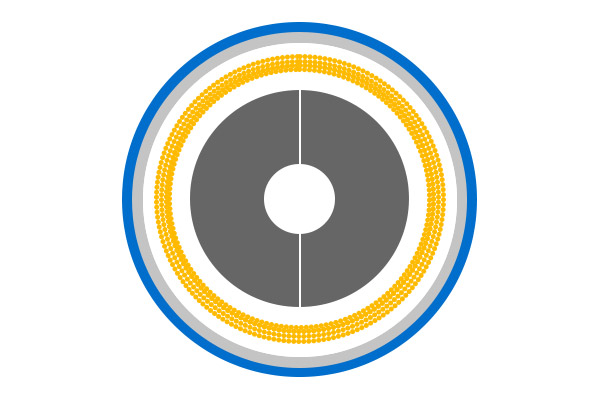
Coreless Type
- Reduces weight and improves efficiency by doing away with iron core.
- Ideal for low inertia and high responsiveness applications.
- Perfect for small, lightweight devices and high-performance motors.
Pole Numbers Options
2 Poles
- Easy to maintain, reasonably priced, and with a straightforward design.
- Faster speed response&higher RPM at lower torque.
- Common in applications requiring high speed, like small fans, toys, or low-torque devices.
4 Poles
- Provides better torque at moderate speeds.
- Offers better torque and smoother operation.
- Ideal for applications needing balanced speed and torque, like tools, vehicles.
6 Poles
- Provides higher torque at lower speeds.
- Increased efficiency at reduced operating speeds.
- Perfect for applications needing strong torque at moderate speeds, like conveyors and machines.
What Can Brushed PMDC Motor Be Combined with?
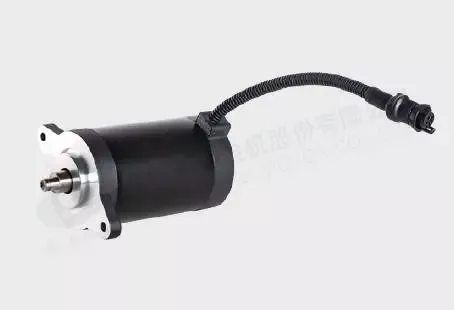
- Gearboxes: To adjust output speed and torque.
- Encoders: For feedback and speed control in closed-loop systems.
- Controllers: To regulate speed, direction, and torque.
- Sensors: For position sensing and performance monitoring.
- Batteries: For portable or battery-operated devices.
- Pulleys and Belts: In applications requiring rotational motion transmission.
- Inverters: For controlling motor speed in variable voltage scenarios.
- Fans: For cooling applications, like in ventilation systems.
Featured Products
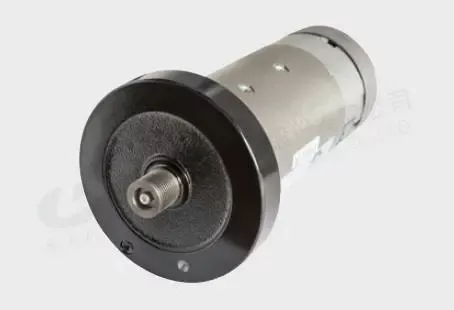
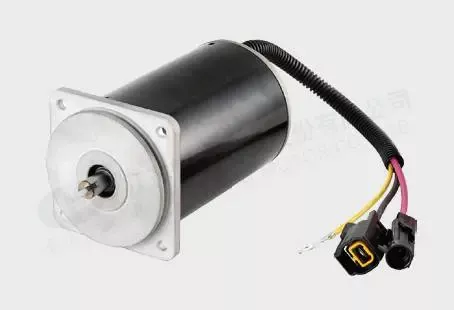
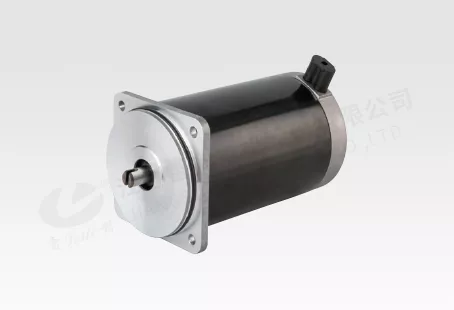
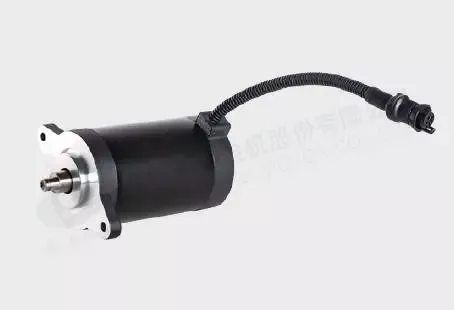
Applications
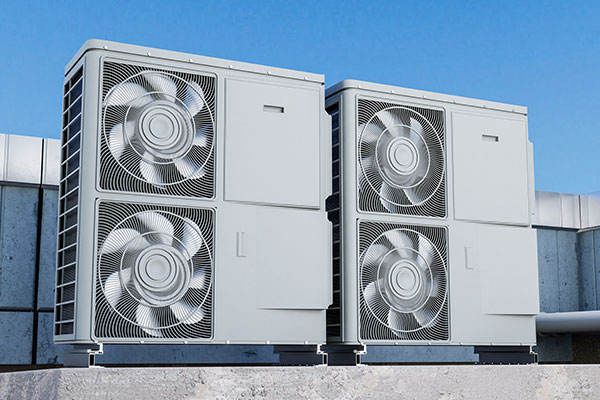
Medical Appliance
- Blowers: Brushed PMDC motors are used in heating, ventilation, and air conditioning (HVAC) systems to drive fans and blowers efficiently.
- Air Conditioners: They drive the fans in air conditioners, ensuring optimal airflow and cooling performance.
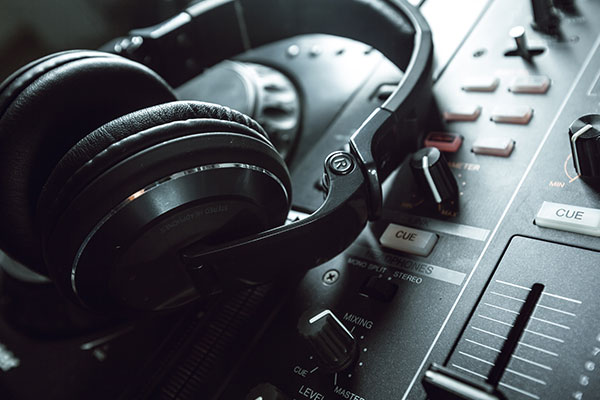
Audio Equipment
- Turntables: Brushed PMDC motors power turntables, offering precise speed control for high-quality sound.
- CD Players: Used in CD players to drive the disc with accurate speed and low noise.
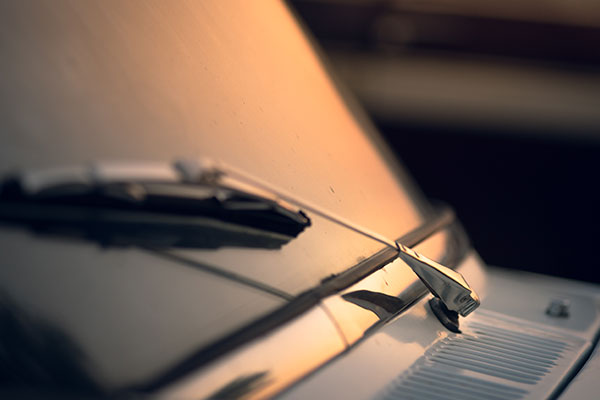
Automotive Applications
- Power Windows: PMDC motors are used to control electric windows, offering reliable, low-maintenance performance.
- Windshield Wipers: These motors power the wipers, ensuring efficient cleaning at various speeds.
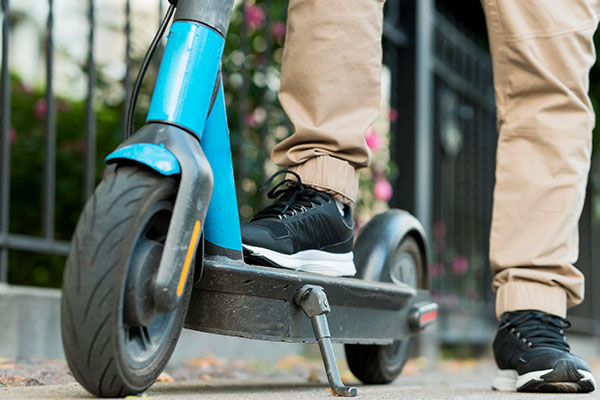
Electric Vehicles (EVs)
- E-bikes & Scooters: Brushed PMDC motors are used in smaller electric vehicles, offering sufficient power for low to moderate-speed needs.
- Golf Carts: These motors provide the necessary power for golf carts and other small EVs with efficient performance at lower speeds.
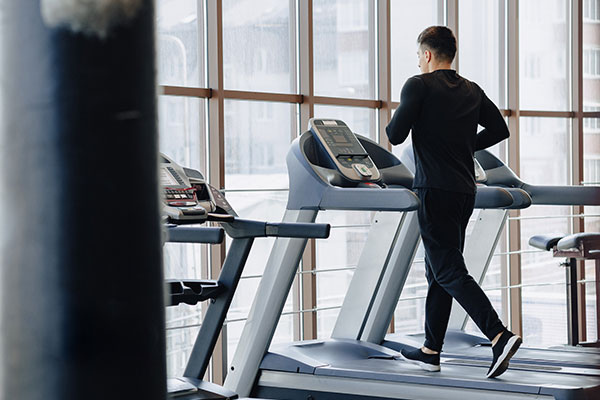
Treadmills
- Drive System: Powers the treadmill belt for smooth, consistent motion.
- Speed Control: Allows precise adjustments to running or walking speed.
- Torque Generation: Provides the necessary torque for various incline levels and resistance.
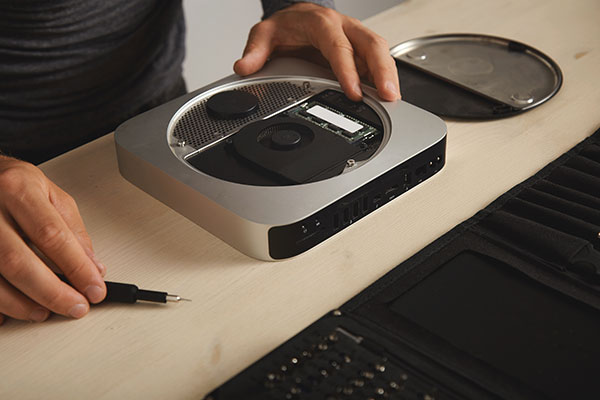
Consumer Electronics
- CD/DVD Players: PMDC motors drive the rotating mechanisms inside CD or DVD players.
- Printers: In inkjet and laser printers, PMDC motors are used to drive paper-feeding mechanisms or the print head.
FAQ
1.Why are brushes used in Brushed PMDC Motors?
Electrical current is transferred via brushes from the motor's stationary stator to its rotating armature.
2.How long do the brushes in Brushed PMDC Motors last?
The lifespan of the brushes depends on the motor's usage, but they typically last several thousand hours before requiring replacement.
3.Can Brushed PMDC Motors be used in high-speed applications?
While they can operate at relatively high speeds, their performance degrades due to friction and wear on the brushes at very high speeds.
4.Are Brushed PMDC Motors suitable for continuous-duty operation?
They are suitable for intermittent or light-duty applications but may require maintenance if used continuously due to brush wear and heat buildup.
5.How is the speed of a brushed PMDC motor controlled?
The motor's voltage can be changed to control speed, or a pulse-width modulation (PWM) controller can be used.