Outrunner Brushless DC Motor
Our outrunner brushless DC motor features high efficiency, torque, and low noise, using permanent magnets for optimal performance.
These motors deliver outstanding speed and responsiveness, making them perfect for high-speed tools, cooling fans, and model aircraft, where rapid rotations and precise control are needed.
- Control Options: Sensored, Sensorless
- Pole Configurations: 2-pole, 4-pole, Multi-pole
- Winding Types: Delta, Star (Y)
- Optional Accessories: Gearbox, Driver, Encoder
- Mounting & Shaft Options: Customizable Configurations Available

Outrunner BLDC Motor Structure
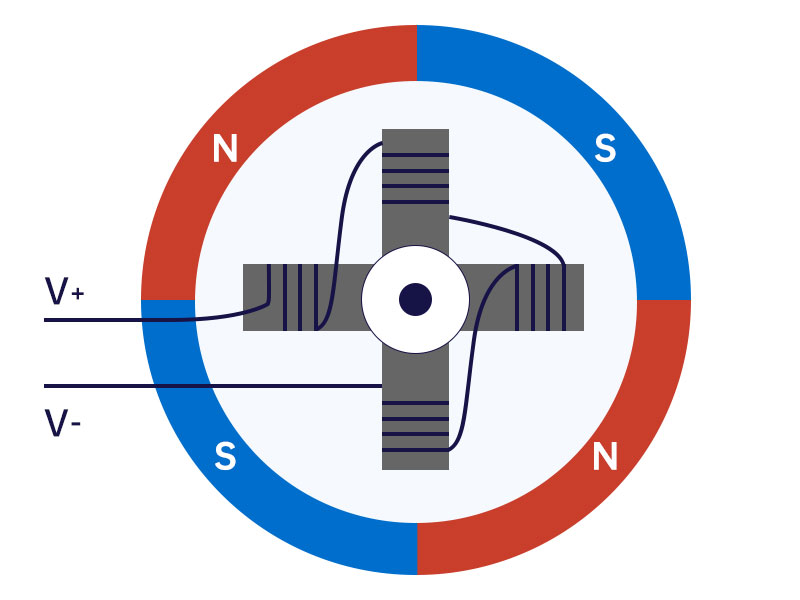
- Our outrunner brushless DC motor consists of a rotor, stator, hall sensors(optional), motor housing, electronic commutator, and bearings for efficient operation.
- Rotor (Outrunner): The outer rotating part containing permanent magnets that generates motion.
- Stator: Stationary part with windings that interacts with the rotor’s magnetic field.
- Hall Sensors: Detect rotor position for accurate electronic commutation and motor control (optional).
- Motor Housing: Protective casing that holds and supports the rotor, stator, and components.
- Electronic Commutator: Replaces traditional brushes, electronically switches current through stator windings.
- Bearings: Support the rotor, allowing smooth, low-friction rotation within the motor housing.
By Shaft Configuration
The single, twin, hollow, and flange shaft variants of our outrunner brushless DC motors provide versatility for a range of mechanical and application requirements.
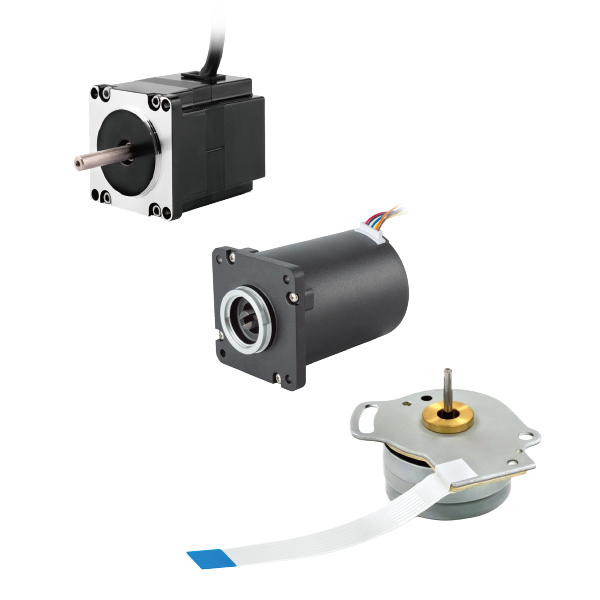
Single Shaft
- Single central rotating shaft for power transmission.
- Compact and efficient, ideal for space-limited environments.
- Available in various sizes for mechanical system flexibility.
Dual Shaft
- Features two shafts for better mechanical integration.
- Ideal for independent rotational movements or drive mechanisms.
- Used in robotics, conveyors, and complex machinery.
Hollow Shaft
- The shaft is hollow to allow cable or component routing.
- Ideal for space and easy cable management.
- Common in precision equipment requiring an unobstructed center.
Flange Shaft
- Shaft with flange for easy, secure attachment.
- Provides stability and support for high-torque applications.
- Ideal for mounting on motor housings or frames.
By Winding Configuration
With Delta or Star (Y) winding configurations, our outrunner BLDC motors maximize torque, efficiency, and performance for a range of voltage and application needs.
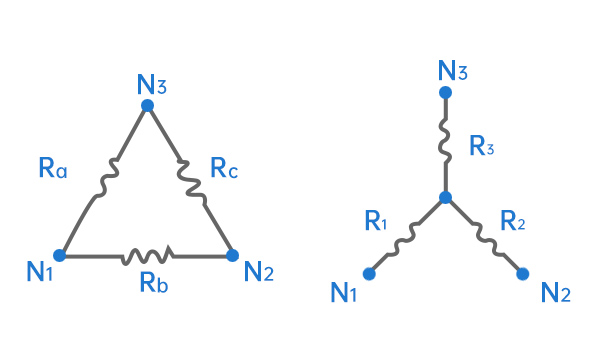
Delta Winding
- Three coils are connected in a triangular configuration.
- Higher current and power at lower voltages.
- Used in high-torque, quick-acceleration applications.
Star (Y) Winding
- Coils are connected in a star shape with a neutral point.
- Higher voltage and efficiency at lower current.
- Suitable for applications requiring smoother operation and lifespan.
By Mounting Type
For safe, effective installation in a range of applications, our outrunner BLDC motors come with front, back, face, flange, shaft, and through-hole mounting options.
Front Mount
- Attaches the motor’s front to the surface securely.
- Secured with radial holes for a firm connection.
- Ideal for applications requiring motor front exposure maintenance.
Rear Mount
- Mounted at the rear, shaft extends outward for coupling.
- Suitable for setups needing rear installation for space.
- Reduces vibration through rearward installation, ensuring stability.
Face Mount
- Bolts the motor’s face plate directly to equipment.
- Provides secure installation when space is limited.
- Best for high-precision applications with minimal alignment.
Flange Mount
- Secures motor to a flat surface using flange bolts.
- Provides secure installation with mechanical support for systems.
- Used for easy integration into existing equipment systems.
Shaft Mount
- Motor’s shaft is fixed directly to surface via coupling.
- Ideal for torque transmission to components like gears.
- Suitable for systems requiring high torque with simplicity.
Through-hole Mount
- Involves a hole passing through the motor’s center.
- Simplifies alignment, providing access for wiring and connections.
- Perfect for applications with space constraints and precise positioning.
Featured Products

24WS/29WS Outer Rotor Brushless DC Motor
- Voltage: 24 V
- Rated Speed: 4100~5200 RPM
- Current: 250~4800 mA

30WS Outer Rotor Brushless DC Motor
- Voltage: 14.4 V
- Rated Speed: 2250 RPM
- Current: 0.85 mA

36WS1-1 Outer Rotor Brushless DC Motor
- Voltage: 12 V
- Rated Speed: 3650 RPM
- Current: ≤ 800 mA

61WZW Outer Rotor Brushless DC Motor
- Voltage: 12V
- Rated Speed: 1200 ± 5% RPM
- Current: ≤ 1.25 A
Applications
Out outer rotor brushless DC motors are used in garden tools, electronics, transportation, industrial equipment, medical devices, and auto parts.

Garden Tools
- Driving garden tools such as lawnmowers, trimmers, and blowers, ensuring low maintenance, quiet performance, and improved energy efficiency for outdoor tasks&maintenance.

Consumer Electronics
- Used in electric fans, water purifiers, massagers, hair dryers, and air purifiers, providing energy-efficient, reliable, and quiet operation in everyday household appliances.
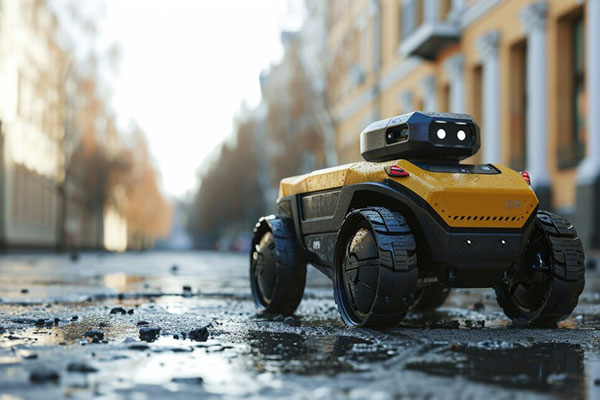
Transportation
- Powering electric bicycles, passenger cars, RC vehicles, drones, and electro-hydraulic forklift trucks, offering smooth and efficient motion for various transportation and mobility solutions.
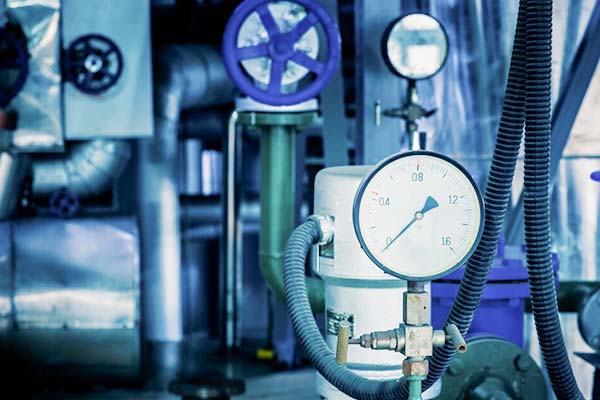
Industrial Equipment
- Utilized in industrial equipment and valve control systems, delivering precise control, high power, and durability for demanding manufacturing and heavy-duty applications.

Medical Equipment
- Found in medical devices like diagnostic tools, ensuring high reliability, low noise, and precise movement in sensitive medical environments.
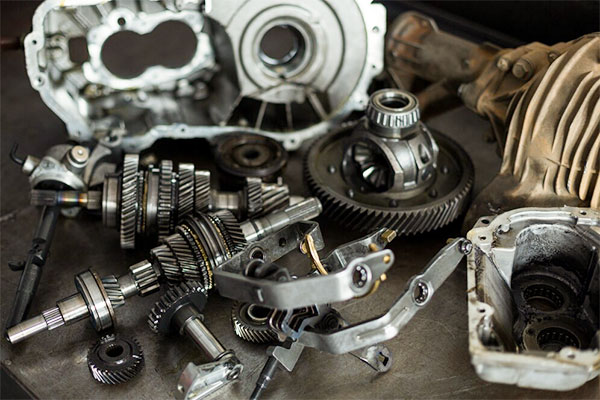
Auto Parts
- Used in electric vehicle components and automotive accessories, providing compact, efficient power for systems requiring dependable motion control and energy efficiency.
FAQ
1.Are Outrunner BLDC Motors More Efficient Than Brushed Motors?
Yes, Outrunner BLDC motors are more efficient than brushed motors because they do not require brushes, increasing performance while lowering heat, friction, and maintenance needs.
2. What types of control mechanisms are available for Outrunner BLDC Motors?
Outrunner BLDC Motors can be controlled using sensored or sensorless methods. While sensorless motors are easier to use and less expensive, sensored motors employ feedback to increase precision.
3. Can our runner-type BLDC motors be used in high-temperature environments?
Our runner-type BLDC motors can indeed be made to function in hot conditions. However, proper cooling solutions are necessary to prevent overheating, which could affect motor performance and lifespan.
4. What is the maximum speed an Outrunner BLDC Motor can reach?
The maximum speed of an Outrunner BLDC motor depends on its size and design, but typically ranges from several thousand RPMs up to 30,000 RPM or higher.
5.What is an Outrunner BLDC Motor's average lifespan?
Outrunner BLDC motors have a long lifespan due to their brushless design, typically lasting tens of thousands of hours if properly maintained, depending on usage and environmental conditions.
6. What are the applications of an Outrunner BLDC Motor?
Outrunner BLDC motors are used in garden tools, electric fans, drones, electric bicycles, massagers, industrial equipment, RC vehicles, medical equipment, air purifiers, and more.